Coal fired power plant – from wikipedia
Coal fired power plant is a power station which burns coal to produce electricity. Central station coal fired power plants are designed on a large scale for continuous operation. In many countries, coal plants provide most of the electrical energy used. Coal fired power stations have machinery to convert the heat energy of combustion into mechanical energy, which then operates an electrical generator. The prime mover may be a steam turbine/engine.
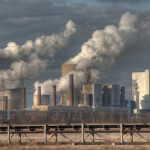
Coal Fired Power Plant in USA-Kentucky
Byproducts of thermal power plant operation must be considered in their design and operation. Waste heat energy, which remains due to the finite efficiency of the Carnot,Rankine, or Diesel power cycle, is released directly to the atmosphere or river/lake water, or indirectly to the atmosphere using a cooling tower with river or lake water used as a cooling medium.
The flue gas from combustion of the fossil fuels is discharged to the air. This gas contains carbon dioxide and water vapor, as well as other substances such as nitrogen oxides (NOx), sulfur oxides (SOx), mercury, traces of other metals, and, for coal-fired plants, fly ash. Solid waste ash from coal-fired boilers must also be removed. Some coal ash can be recycled for building materials.[1]
Coal fired power stations are major emitters of CO2, a greenhouse gas which according to a consensus opinion of scientific organisations is a contributor to global warming. Per unit of electric energy, brown coal emits about 3 times as much CO2 as natural gas, and black coal emits about twice as much.
Carbon capture and storage of emissions is not expected to be available until technology is safe and deployable.
Basic concepts
In a fossil fuel power plant the chemical energy stored in fossil fuels such as coal, fuel oil, natural gas or oil shale and oxygen of the air is converted successively into thermal energy, mechanical energy and, finally, electrical energy. Each fossil fuel power plant is a complex, custom-designed system. Construction costs, as of 2004, run to US$1,300 per kilowatt, or $650 million for a 500 MWe unit. Multiple generating units may be built at a single site for more efficient use of land, natural resources and labour. Most thermal power stations in the world use fossil fuel, outnumbering nuclear, geothermal, biomass, or solar thermal plants.
The Pain
The coal-burning power plants are the units with the highest emission, so they are likely to be closed because of the climate changes.
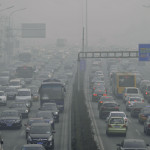
Extreme air pollution in China
The biggest limit of energy production of steam engines is the Carnot cycle ƞ=(Tmax-Tmin)/Tmax. The efficiency even of the most modern coal power plants is ~30%. It means that ~70% of the produced energy gets out to the air when burning coal, and that means the same amount of the unnecessary CO2 emission as well. The efficiency of locomotives is even worse.
Nowadays the Coal Fired Power Plants are under the highest pressure to decrease its emissions, or retire if they can not meet the strict operation criterias.
We see that the 2 big player countries are in deep crisis: U.S. & China.
The planned 72GW power plantsare retiring in the U.S.A. nowadays and within few years all of them will be closed.
Nowadays day-by-day are coming fresh news from China about the higher and higher air pollution record values. Despite of this fact they are planning to build 565 new Coal Fired Power Plants in the near future!
The problems of the Coal Fired Power Plants:

1,000 MW
- low efficiency – average 30%
- low profit rate – 10-13%
- High pollution emission – NOx, COx, SOx, soot, and so many other polluter solid materials
- Low popularity – rising of renewable energy technologies
The opportunities of Coal Plants:
- coal stock worldwide: more than 400 years
Chinese Coal Power Plant
- development or re-construction of power stations
- decrease the emission of plant
What would be the best solution?
- increase the efficiency and
- treat the emissions to near ZERO and
- increase the profitability after the re-construction of coal plant
Many experts think that this (best) solution is impossible.
SMARTii team has proven, during an experimental test that it is possible.
We made the first steptowards the solution, by proving that we can reach higher efficiency, with reaching higher pressure in shorter time with burning the same weight of coal in the same boiler.
Thanks to SER material and technology.